Debinding and Sintering of Ceramics
BROTHER FURNACE
2024-12-05 22:48
Ceramic materials are widely recognized for their exceptional mechanical properties, thermal stability, and resistance to wear and corrosion. These qualities make them indispensable in the aerospace, electronics, and healthcare industries. However, producing high-quality ceramic components requires meticulous processes, with debinding and sintering critical steps determining the material's performance and durability. This article delves into the principles, methods, and significance of ceramic debinding and sintering in manufacturing.
What Is Ceramic Debinding?
Ceramic debinding is the process of removing binders and other additives from ceramic green bodies before sintering. Binders, typically organic or inorganic substances, are introduced during the forming process to enhance powder cohesion and improve the mechanical strength of the green body.
Primary Goals of Debinding:
Binder Removal:
Eliminate all binder components to create optimal conditions for subsequent sintering.
Defect Prevention:
Avoid cracks, pores, or warping caused by residual binders decomposing during sintering.
Enhanced Sintering Results:
Establish a uniform pore structure that facilitates densification.
What Is Ceramic Sintering?
Ceramic sintering involves heating the green body to a temperature below its melting point to facilitate particle bonding through physical and chemical processes. This transforms the porous green body into a dense ceramic component with superior mechanical properties.
Primary Goals of Sintering:
Densification:
Minimize porosity and enhance material density.
Mechanical Property Enhancement:
Improve the strength, hardness, and toughness of the ceramic.
Functional Optimization:
Enhance properties such as thermal conductivity, electrical resistance, and chemical stability.
The Relationship Between Debinding and Sintering
Debinding and sintering are interconnected processes in ceramic manufacturing. Effective debinding lays the foundation for successful sintering, as residual binders can lead to the following issues
Cracks or Pores:
Residual binders decompose during sintering, releasing gases that may cause cracks or pores.
Chemical Contamination:
The remaining binders may react with the ceramic material, compromising its final properties.
Uneven Densification:
Residues can create temperature inconsistencies during sintering, affecting the material's density and strength.
To address these challenges, many manufacturing processes integrate debinding and sintering into a single operation through controlled multi-stage heating.
Recommended Debinding and Sintering Furnace
Brother Furnace has successfully provided ceramic debinding and sintering solutions to customers worldwide. One of the most recommended options is the elevator-type debinding and sintering furnace, which integrates both processes for convenience and efficiency.
Key features of this furnace include
High-Temperature Capability
Maximum operating temperature of up to 1800°C, suitable for most ceramic applications.Customizable Chamber Size
Tailored to accommodate various product dimensions and production scales.Superior Ceramic Quality
Produces ceramics with high density, exceptional strength, and outstanding resistance to wear and heat.
This furnace is ideal for electronics, aerospace, and healthcare industries, where high-performance ceramics are essential. Click here to learn more.
Applications of Debinding and Sintering
Debinding and sintering processes are integral to the production of ceramic components across numerous industries:
Electronics Industry
Used in manufacturing capacitors, insulators, and semiconductors requiring high precision.
Aerospace Industry
Fabrication of components like thermal shields and turbine blades with high thermal stability and strength.
Medical Industry
Creation of dental implants, bioceramics, and other biocompatible materials.
Energy Sector
Applications in fuel cells and battery components rely on durable and conductive ceramics.
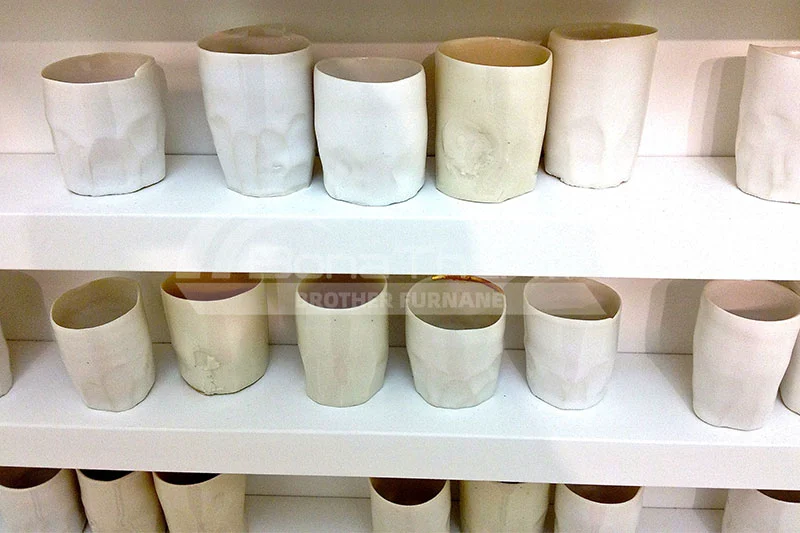
Conclusion
This article has explored the principles and importance of ceramic sintering and debinding in modern manufacturing. If you are in need of advanced equipment for ceramic sintering or debinding, consider Brother Furnace. Share your requirements with us, and our team of expert engineers will provide customized solutions tailored to your needs!